医疗器械公司如何用 400 分体式机床线切割实现内窥镜镜头座高精度加工
一、战挑重案例分析:医疗与工业的双重挑战
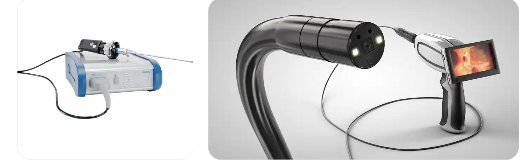
某医疗器械:题难大两公司在开发新一代医用内窥镜时,遇到了两大难题:
1.医用内窥镜镜头座:需容纳微米级光学元件,要求孔位同轴度误差≤±0.003㎜,表面粗糙度 Ra≤0.7-1.4μm,且材料(钛合金)易受热变形;
2.风力发电机关键零部件:需加工高强度合金叶片榫头,复杂曲面的轮廓精度要求达 ±10μm,传统铣削工艺效率低下。
传统加工瓶颈:
· 铣削刀具易磨损,导致尺寸一致性差;
· 电火花成型加工效率低,且难以处理深窄槽结构;
· 激光切割存在热影响区,可能破坏材料性能。
二、400 分体式机床线切割的破局之道
智凯数控提供的 400 分体式机床线切割系统,通过三大核心技术突破了上述难题:
1.超精密运动控制
采用双驱直线电机 + 光栅尺闭环系统,定位精度达 ≤±0.003㎜;
案例数据:医用内窥镜镜头座孔位同轴度提升至 3μm,合格率从 72% 提升至 98%。
2. 自适应脉冲电源技术
实时监测放电状态,动态调整脉冲参数;
材料热影响区减少至 10μm 以内,完美应对钛合金等敏感材料。
3. 智能路径规划系统
通过 AI 算法优化切割轨迹,风力发电机叶片榫头加工效率提升 40%;
复杂曲面加工表面粗糙度稳定在 Ra≤0.7-1.4μm,无需后续抛光。
三、数据验证与行业趋势
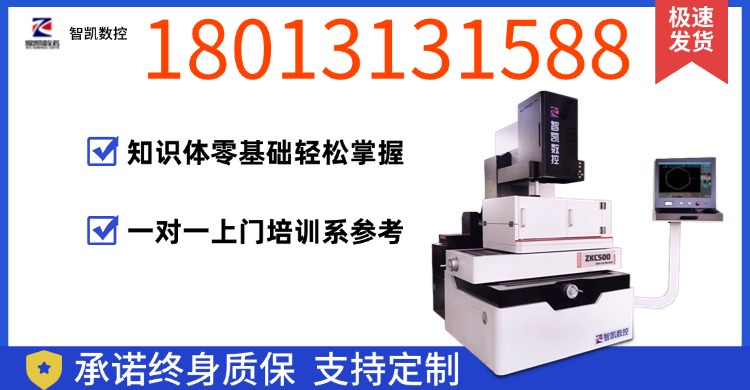
1.生产效率:单台设备日均处理医用镜头座 200 件,较传统工艺提升 2.5 倍;
2.能耗优化:采用伺服节能系统,单位能耗降低 28%;
3.行业应用:除医疗与风电外,该技术已成功应用于航空航天(如卫星传感器支架)、半导体(硅片精密切割)等领域。
行业观点:
“线切割技术的进化,本质是精密制造的‘减法哲学’—— 用最小的能量输入实现最高的材料去除精度。” 某国际医疗设备认证机构专家指出,“智凯数控的模块化设计与远程运维系统,正在重新定义高端加工设备的服务标准。”
当传统线切割遭遇效率瓶颈时,智凯第三代智能修刀技术正为3576家客户节省15%钼丝损耗。您的加工痛点,我们早已用模块化设计给出了答案:自研恒温原色加工电源系统应对复杂材料,快速响应确保7×24h稳定运转。现在咨询可免费领取《中走丝加工参数优化白皮书》,智凯工程师团队已就位,三分钟内为您定制降本增效组合拳。"欢迎松潘县、九寨沟县、茂县、若尔盖县、汶川县、马尔康市、黑水县、阿坝县、理县、金川县、红原县、壤塘县、小金县等地朋友咨询.。